Progressing Schedules through
Integrated Completions and Commissioning Services
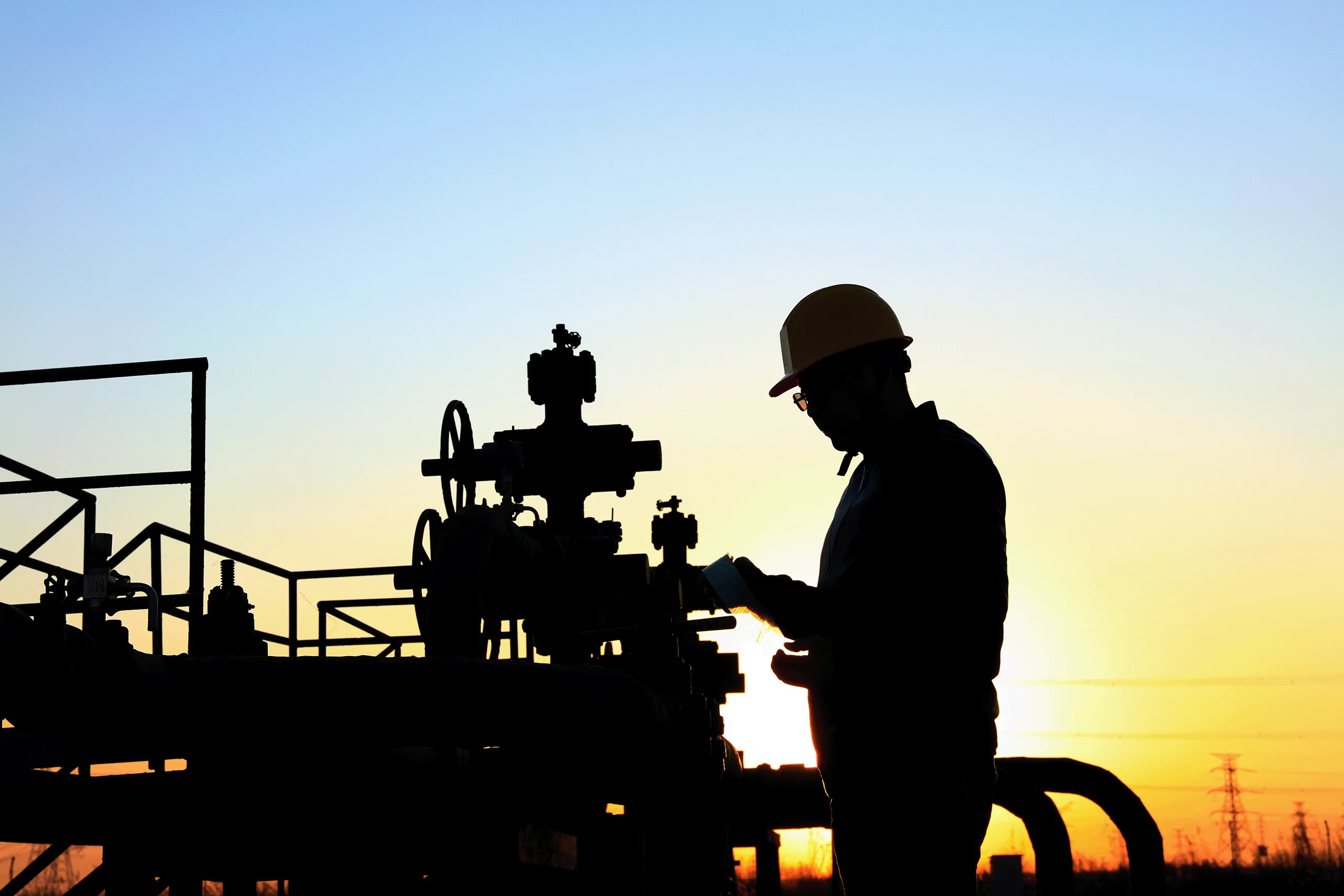
The client was twinning a major pipeline to expand its capacity nearly three-fold. The new pipeline runs parallel to an existing pipeline, which was built decades ago, and will support the country's ability to ship its oil products to global energy markets.
CLIENT PROFILE: PIPELINE COMPANY TRANSPORTING OIL PRODUCTS TO CANADA'S COASTLINE
The project, the largest in the pipeline’s history, involved adding new facilities and modifying existing ones, including pump stations, terminals, and a dock at a marine terminal.
The Canada Energy Regulator (CER) Act requires CER permission prior to putting a pipeline into service after construction has been completed. The client required a transition from the mechanical stage through to commissioning and business readiness and a phased approach to construction, commissioning, and startup. This phased approach ensured approvals during each stage of construction were completed in a timely manner.
TRUE NORTH SOLUTIONS' APPROACH AND HIGHLIGHTS
True North Solutions was initially engaged by the client to participate in a workshop to provide guidance and strategies to effectively progress mechanical completion, commissioning, and business readiness, ultimately helping the client realize in-service and revenue.
Following this initial engagement, True North was subsequently retained by the client to serve as a commissioning resources service provider to assist with execution and document commissioning and startup activities. In this role, True North supported:
- Safety
- Records management
- Mechanical completion turnover
- Master punch list administration
- Document management, including as-built piping and isometric diagrams, single line diagrams, and test equipment calibration certificates
True North provided personnel to support these activities to perform equipment installation verification, systems setup and configuration, systems energization and operational testing, critical systems cause and effect testing, documentation & witness, and transfer to Operations. This responsibility applied to assets, including but not limited to 12 new pump stations, 19 new tanks with metering manifolds, auto samplers, oil quality/spec metering at four different terminals, 25 new sending/receiving traps, deactivating and decommissioning within existing facilities, loading dock complex with total of three Aframax-capable berth faces, utility dock and ancillary components with mainline block valves, scraper traps, pressure reduction or relief stations, containment, power lines, access roads, and temporary infrastructure.
To further manage project risks, facilitate a swift transition from mechanical completion through to commissioning and business readiness, and mitigate stakeholder concerns about scheduling, the client engaged True North to conduct a quality, care, and preservation audit to measure the client’s engineering, procurement, and construction quality, care, and preservation processes against actual work documentation, drawings, data sheets, and physically installed equipment assemblies.
In conjunction with the quality, care, and preservation review and audit, True North performed an engineering review against standards and inspection and test reports to determine potential engineering and design gaps, which would require variances or additional engineering and procurement support.
Neither the audit, nor the engineering review were discipline-specific and required collaboration with the client’s subject matter experts (SMEs) to support walkdowns, inspections, and reviews to facilitate improved accuracy of information and documentation related to the quality, care, and preservation audit and engineering report deliverables.
CONCLUSION
True North mobilized more than 50 personnel with a 95% retention rate for project commissioning, startup, audit, and engineering review services.
Our senior program management and engineering SMEs provided guidance on quality assurance, commissioning and procurement processes, engineering design, and schedule management while supporting the client in mitigating technical and project execution risks related to commissioning and startup that could result in further mechanical completion schedule delays and cost increases.
True North’s unbiased assessments and strategies favorably impacted the client’s mechanical completion progress and schedule.
For more information on how True North Solutions can transform your commissioning activities, please contact us.
TRUE RELATIONSHIP ADVANTAGE
Review our case studies to see real-world examples of how our solutions benefit our clients.